Cement Grade, Proportions Types of cement use,a strong building material, comes in different types like Portland, used for most constructions,
Cement and Types of cement, a strong building material, comes in different types like Portland, used for most constructions, and special ones like rapid-setting cement. Let’s learn about them simply.
Table of Contents
There are two processes of cement manufacturing
1. Dry process
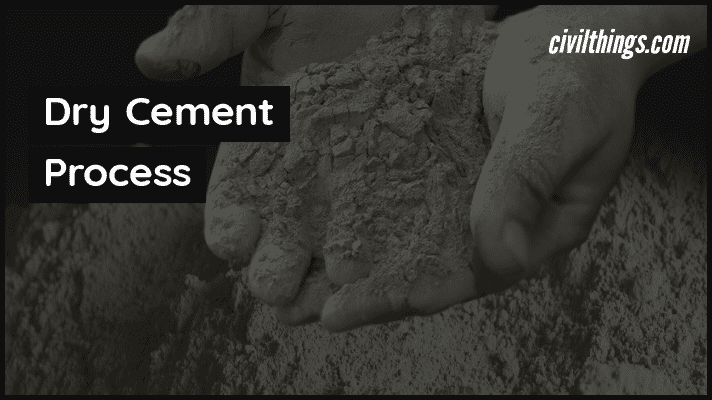
The dry process of making cement involves crushing and grinding raw materials like limestone and clay to create a fine powder. This powder is heated in a kiln to make clinker, which is then ground into cement.
2. Wet process
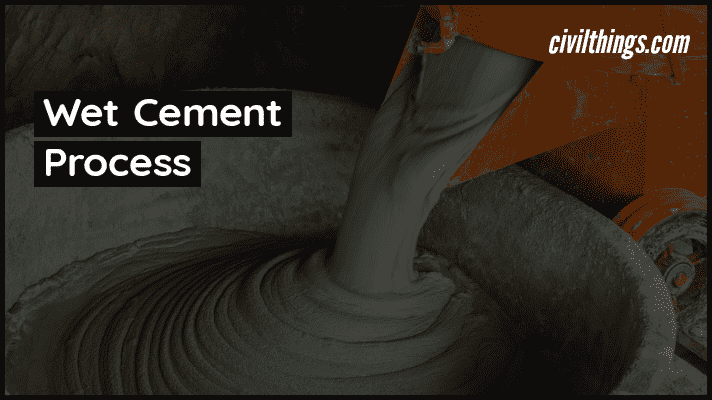
The wet process of making cement involves mixing limestone and clay with water to create a paste. This paste is then heated in a kiln to make strong cement for building things.
Cement Cantent
The raw material used for the manufacturing of cement is mainly out of lime, silica, alumina, and iron oxide these oxides interact with what another is the clinker at 5°C temperature. Thigh to form
more complex compound approximate compaction limits of ordinary Portland cement.
TABLE:
Oxide | %Cantent | ||
Lime | Cao | Calcium Oxide | 60-67 |
Silica | Sio2 | Silica Oxide | 17-25 |
Alumina | Al2o2 | Aluminum Oxid | 3.0-8.0 |
Iron Oxide | Fe2O3 | 0.5-6.0 | |
Magnesium Oxide | MgO | 0.1-4.0 | |
Alkaline | K2oNa2o | 0.4-1.4 | |
Sulfur OXide | So3 | 1.3-3.0 |
In Indian standard specifications of 33-grade cement IS -269-1990 ( cement).
Specified the following chemical requirements:-
A) Ratio of the percentage of lime 2% silica, alumina, iron oxide know type saturation factor.
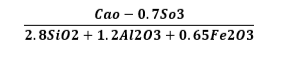
Non greater than 1.02 not less than 0.66
B) The ratio of the percentage of alumina to that iron oxide is not less than 0.66.
C) The weight of insoluble residual is not more than 4%.
D) The weight of magnesium is not more than 6%.
E) Total sulfur content calculation as sulphuric when unhydrant ( SO3) not more than 2.5%
F) Total loss ignition not more than 5%.
As mentioned earlier the side present in raw material when subjected to high temperature combines to form another complex compound the identification of measure compound is earlier based on arranged bugs hence it is called a bugs compound.
TABLE:
Name of Compound | Formula | Abbreviation |
silicate | 3cao. Sio2 | C3A |
Dicalcium silicate | 2cao. Sio2 | C2s |
Tricalcium Aluminate | 3cao Al2o3 | C3A |
Tetracalcium Alumn Feritie | 4Cao. Al2o3 Fe2o3 | C4AF |
FORMULA:
C3S = 4.07 (Cao) – 7.6 (Si) – 672 (Al2O30) – 1.43 (Fe2O3) – 2.8 (So3)
C2S = 2.87 (SiO2) – 0.754 (3Coo – Sio2)
C3A = 2.65 (Al2o3) – 1.69 (Fe2O3)
C4AF = 3.4 (Fe2O3)
Hydration of cement
Unhydrated cement does not mine fine and coarse aggregate required orders properly only when mixed with water the chemical required that takes place between cement and water is referred to as the hydration of cement.
Heat of hydration
The reaction of cement with water is extropy the response releases several heat this released heat is called the heat of hydration.
Products are:-
1. Calcium silicate hydrate – 50-60 % of the scan volume.
2. Calcium hydroxide – 20-25 % of the volume of the can.
3. Calcium eliminates hydrates.
water required for hydration
It has been throughout earlier seat 35 required 24% of water by weight of cement of weight of cement and C2S world 21% Average of 23% of water by weight of cement is required for chemical reaction with a Portland cement compound this 23% of water chemically combines with cement, therefore, it is called bound water.
- A creation quantity of water is embedded within the jail process; This water is called a
gel water. - It Is said bound water and gain water entirely to each other .
- In the quantity of water in data to fill up the gain process, the formation of gain itself stops, and if the formation of games stops there is no question of gain course being present.
- It has been further estimated that about 50% by weight of cement is required to fill up the
game process. - Hence a total of 38% of water by weight of cement is required for the complete chemical
reaction and occupied within the gel process. - Increase in water case considerable capability cavity.
Cement Grade and Proportions also Common Use
Concrete Mix Designation (Cement Grade) | Proportions (Cement:Sand:Aggregate) | Common Use |
---|---|---|
M5 | 1:5:10 | Paving blocks, non-structural applications |
M10 | 1:3:6 | Plastering, flooring |
M15 | 1:2:4 | Foundation, footing |
M20 | 1:1.5:3 | Slabs, beams, columns |
M25 | 1:1:2 | High-rise buildings, heavy-duty structures |
M30 | 1:0.75:1.5 | Industrial structures, bridges |
M35 | 1:0.5:1 | High-performance concrete |
M40 | 1:0.4:0.8 | Prestressed concrete members |
M45 | 1:0.35:0.7 | Specialized structural applications |
The numbers in the mix designation (e.g., M15, M20) represent the characteristic compressive strength of the concrete in megapascals (MPa) at the 28-day curing period.
The proportions represent the ratio of cement to sand to coarse aggregate by volume.
For example, for M15 concrete mix:
1 part cement
2 parts sand
4 parts coarse aggregate
This mix is commonly used for general construction purposes like foundations and footings.
Types of cement
1. Ordinary Portland cement (OPC).
2. Rapid hardening portland cement (RHPC)
3. Extra-rapid hardening Portland cement.
4. Portland blast-furnace cement.
5. Low-heat Portland cement.
6. Sulphate resisting Portland cement.
7. White Portland cement.
8. Coloured Portland cement.
9. Super-sulphate cement.
10. Masonry cement.
11. Expansive cement.
12. Oil-wet cement.
13. Hydrophobic cement.
14. Pozzolana cement.
15. High-Alumina cement.
16. High-strength cement.
17. Acid-resisting cement.
18. Quick setting cement.
19. Blended cement.
Also Read,
1. BASIC INGREDIENTS OF CONCRETE MIX
2. TOP 10 PRINCIPLES OF PLANNING | VARIOUS CONSTRAINTS
Question
1. What is the manufacturing process of cement?
2. Enlist types of cement?
3. What are the chemical requirements?
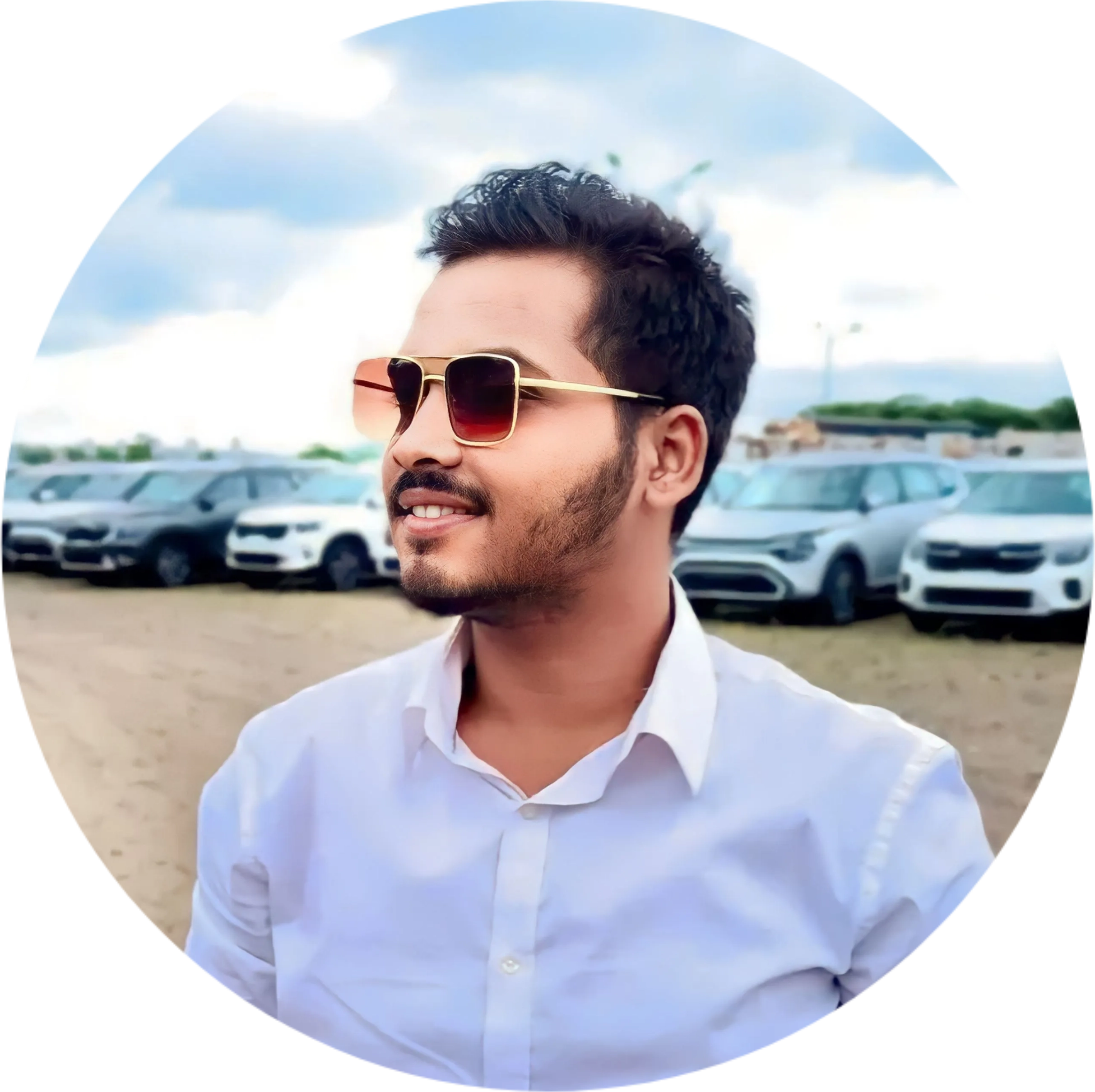
Hi! I’m Sandip, a civil engineer who loves sharing about Civil Engineering & new ideas and tips. My blog helps you learn about engineering in a fun and easy way!